Grain Dust Explosions Are Preventable, So Why Are They Still Happening?
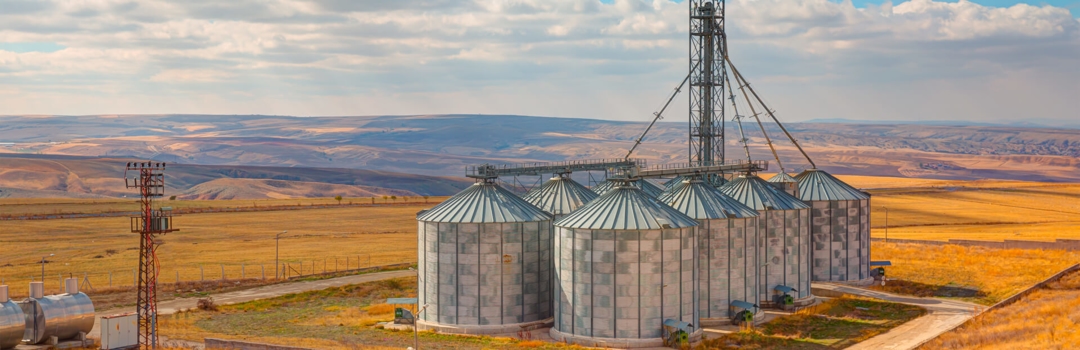
A little after 9 in the morning on December 22, 1977, a thunderous blast shook homes and businesses throughout Greater New Orleans. Buildings rattled and windows shattered in the Uptown neighborhood and as far away as west Jefferson Parish. Eyewitnesses reported seeing a gigantic fireball explode several hundred feet over the Westwego riverfront, followed by an enormous “mushroom cloud” of smoke and debris. The debris—mostly comprising tiny particles of grain and dust—showered down on the river, streets, and buildings below.
Just three days before Christmas, an elevator at the Continental Grain Company had exploded, killing 36 people and injuring more than 70 others. The blast was so massive, it blew the tops off 45 grain silos and caused the facility’s 250-foot main storage tower to collapse onto an office building below. Employees, many of whom were not even scheduled to work that day but were there to pick up Christmas turkeys—a gift from the company—were buried beneath a pile of rubble 120 feet high. It took emergency responders several hours to get the flames under control and 10 days to remove the last of the victims from the burning wreckage.
To this day, the exact cause of the explosion is not fully known, though most experts believe it was likely the result of a spark in one of the conveyer belts, either caused by a short circuit or static electricity. That, combined with one of the coldest winters in the past several decades, led to what remains the deadliest grain industry disaster in American history.
Grain Dust Explosions: A History of Negligence
The Continental Grain Elevator explosion was an incredible tragedy, but it is far from the only grain dust explosion in modern history. In fact, that very same week, three other grain elevator blasts—in Illinois, Mississippi, and Texas—resulted in 17 deaths. And, a little more than 20 years later, in 1998, the DeBruce Grain Elevator explosion in Wichita, Kansas, caused the death of 7 workers, trapped 10 others, and resulted in extensive damage to what was then the largest grain elevator in the world.
Each of these incidents spurred separate investigations to determine exactly what went wrong. The results were alarming.
In many cases, these explosions were the result of negligence, from lack of regulations to poorly maintained machinery. After the disaster in Westwego, the Occupational Health and Safety Administration (OSHA) fined the Continental Grain Company more than half a million dollars for numerous safety violations. Two decades later, DeBruce Grain paid $685,000 in fines but admitted no fault in the explosion that claimed over half a dozen lives.
Grain dust explosions are completely preventable. In fact, a report on the DeBruce Grain Elevator explosion found that the company ignored key safety standards, including allowing an accumulation of excess grain powder—an essential element that led to the deadly blast. With the right precautions, these tragedies can not only be mitigated but eliminated entirely.
What Is Grain Dust?
Grain dust is a fine, powdery substance made up of tiny particles that are released during the handling, processing, and transportation of various types of grains, including wheat, corn, oats, barley, and soybeans. This dust can come from the grain kernels themselves, but it also includes bits of plant material, insect parts, mold spores, pesticide residues, and other contaminants.
Grain dust is a common byproduct of everyday agricultural and industrial activities, such as:
- Drying, grinding, milling, or otherwise processing grain
- Loading or unloading grain from trucks, silos, or elevators
- Moving grain with conveyer belts, augers, or pneumatic systems
- Sweeping spilled grain or operating fans or blowers
Although it may seem harmless, grain dust is highly combustible under the right conditions. When high concentrations of grain dust are suspended in the air in a confined space and exposed to a heat source or spark, it can ignite. Grain dust is considered one of the most hazardous substances found in agricultural work environments due to its combustible nature and its potential to cause explosions in grain handling facilities.
How Do Grain Dust Explosions Happen?
Grain dust explosions are violent, fast-moving events that often cause catastrophic damage. To understand how they happen, we need to look at two key factors: the explosiveness of grain dust itself and the conditions that allow it to ignite.
Grain dust is made up of microscopic organic particles, including tiny fragments of grain, chaff, husks, and mold spores. These particles are rich in starch and other carbohydrates, which act as fuel when suspended in the air. Because of their small size and high surface area, they can ignite easily when exposed to heat or a spark. Once ignited, they burn rapidly, releasing gases that expand and create shockwaves. This is what causes the volatile force that leads to grain dust explosions.
The National Fire Protection Association (NFPA) notes that many agricultural dusts, including those from wheat, corn, oats, and soybeans, are classified as combustible dusts, or substances that can ignite and explode when dispersed in the air in sufficient quantities.
Common Causes of Grain Dust Explosions
Grain dust explosions don't happen randomly; they require five specific elements to be present at the same time. This is known as the “dust explosion pentagon,” a concept developed by fire safety experts to explain how these events occur.
The dust explosion pentagon consists of five key elements:
- Combustible Dust: Explosions require fuel. In this case, the fuel is grain dust, which is highly combustible when in a fine particulate form.
- Ignition Source: A spark, flame, or heat source is needed to start the explosion. Even small sources like static electricity, friction from moving parts, overheated bearings, or welding equipment can trigger ignition.
- Oxygen: Oxygen is necessary to support combustion. Because it is present in the air, oxygen is always a factor when dust particles become airborne.
- Dispersion of Dust Particles: The dust must be suspended in the air at the right concentration. If the dust is simply sitting in a pile, it may burn but won’t explode.
- Confinement: When the dust cloud is enclosed within a structure—like a silo, grain elevator, or duct system—the pressure from the combustion builds up rapidly. This pressure is what causes violent explosions.
If all five elements are present, a single small event—such as a spark from a misaligned conveyor belt or a hot motor bearing—can ignite the dust cloud. The initial explosion can then disturb more dust that’s settled on surfaces, creating a chain reaction of secondary explosions. In fact, secondary grain dust explosions are often more destructive than the first, as they involve larger areas and higher dust concentrations.
Small Ignition Sources Can Have Big Consequences
One of the most dangerous aspects of grain dust explosions is how little it takes to ignite them. Research by the U.S. Chemical Safety Board (CSB) and OSHA has shown that ignition sources as small as a spark from static electricity or friction from a misaligned belt can be enough to start an explosion.
Common sources of ignition in grain handling facilities include:
- Overheated bearings or motors
- Metal-to-metal friction (such as a jammed auger)
- Welding or cutting operations
- Electrical shorts or equipment malfunctions
- Hot surfaces from dryers or other machinery
Even dust layers as thin as 1/32 of an inch (about the thickness of a paperclip) spread across a large surface can contribute enough fuel for a secondary explosion.
When & Where Grain Dust Explosions Are Most Likely to Occur
Grain dust explosions don’t happen arbitrarily. They tend to occur in specific types of facilities and during certain times of the year.
Some high-risk areas include:
- Grain Elevators: Grain elevators store and process large volumes of grain, which can generate significant amounts of grain dust. Combined with the fact that grain elevators are confined spaces by nature, this leads to a heightened risk of explosions occurring in these structures.
- Silos: Used for storing large quantities of grain, silos can accumulate excess dust over time. This is especially true if they are not regularly cleaned or if safety standards are ignored.
- Mills: These facilities house equipment used to grind grain into flour or meal. This process produces fine dust particles, which can become airborne and, under the right circumstances, lead to explosions.
- Conveyor Belts: These systems transport grain within elevators, mills, and other facilities. This not only generates dust, but the friction and movement can provide heat sources or sparks that may ignite particles.
In 2024, Purdue University's annual report documented nine grain dust explosions in the U.S., occurring in various facilities from feed mills to grain elevators, an ethanol plant, and a corn processing plant.
Grain dust explosions also are more prevalent during certain seasons, particularly:
- Harvest Season: The increased handling and processing of grain during harvest time typically results in more dust.
- Dry Weather Conditions: Low humidity levels can cause dust particles to become more easily airborne.
- Winter: When it’s cold, there tends to be less humidity and more static electricity. These factors can increase the risk of explosions in grain facilities.
When these factors align and occur in areas where conditions are ripe for grain dust explosions, the results can be catastrophic. Employers must take the necessary steps to protect their workers’ health and safety.
How Can Grain Dust Explosions Be Prevented?
Grain dust explosions are preventable—but only with a proactive, multi-faceted approach that addresses the specific conditions leading to these events. The following strategies can significantly reduce the risk of an explosion in grain-handling facilities.
General Housekeeping & Dust Control
One of the most effective ways to reduce the risk of grain dust explosions is by controlling dust accumulation.
Employers and grain processing companies should ensure that:
- Facilities Are Routinely Cleaned: Grain facilities should be cleaned on a regular schedule to prevent dust from building up on floors, rafters, and machinery. A layer of dust no thicker than a dime (1/32 of an inch) can cause a catastrophic explosion if spread over just 5% of a room.
- Employees Use Explosion-Proof Vacuums: Employers should equip workers with up-to-date, well-maintained industrial vacuums that are certified for combustible dust. These vacuums are specifically designed to prevent the ignition of dust particles during collection.
- Workers Avoid Using Compressed Air: Blowing dust with compressed air is dangerous, as it can suspend fine particles into the air and create an explosive dust cloud. OSHA strongly discourages this practice unless all ignition sources are eliminated and proper ventilation is in place.
Ventilation & Air Filtration
Good airflow keeps dust levels low and helps prevent dangerous concentrations.
This can be achieved with:
- Dust Collection Systems: Grain companies and facilities managers should install properly maintained dust collection equipment near dust-generating machinery, such as grinders, mills, and conveyor transfer points. These systems capture airborne dust before it can settle or accumulate.
- Maintaining Safe Dust Levels: Continuous air quality monitoring and airflow management help prevent dust concentrations from reaching explosive thresholds. Employers should implement and enforce policies that help maintain safe dust levels in facilities where grain dust is or could be present.
Maintenance & Monitoring
Poorly maintained equipment can create ignition sources through heat or friction. To prevent potential disasters, employers should ensure that all equipment is routinely inspected and maintained. Regular checks help identify worn parts or potential hazards before they cause a problem. This includes checking for dust buildup on hot surfaces or moving parts.
When conducting routine inspections and maintenance, workers should pay close attention to bearings, motors, belts, and conveyors. Overheated bearings or slipping belts can generate sparks or heat that ignite dust clouds.
Ignition Source Control
Even the smallest spark can trigger a dust explosion in the right conditions. To combat this, employers must establish aggressive ignition source control processes.
These might include:
- Regular Equipment Grounding and Bonding: All conductive equipment should be properly grounded to prevent static electricity buildup, which is a common ignition source in dry, dusty environments.
- Use Intrinsically Safe Systems: Explosion-rated or inherently safe electrical systems are designed to operate safely in flammable environments. This can significantly reduce the risk of grain dust explosions.
Emergency Planning & Training
In addition to taking all necessary steps to prevent explosions from happening, employers should make sure that workers are properly trained on disaster prevention and emergency response. Preparedness can make the difference between a minor incident and a major disaster.
All workers should receive regular training on dust hazards, proper cleaning methods, emergency procedures, and how to recognize early warning signs of ignition risks. Where appropriate, employers should install explosion suppression or isolation systems. These can detect and quench a developing explosion before it propagates through ductwork or interconnected equipment.
Employers should also make sure facilities have clear, accessible evacuation routes and well-communicated emergency plans. Regular drills and clear signage help everyone respond quickly in case of an emergency.
Beyond Explosions: The Respiratory Risks of Grain Dust
In addition to causing deadly explosions, grain dust can also lead to serious respiratory illnesses when inhaled. Agricultural and industrial workers in grain processing facilities are especially at risk.
Some of the common conditions correlated with grain dust exposure include:
- Allergic alveolitis (“farmer’s lung”)
- Asthma
- Chronic obstructive pulmonary disease (COPD)
- Chronic bronchitis
- Conjunctivitis (itchy or watery eyes)
- Coughing, often chronic and/or severe
- Difficulty breathing
- Flu-like symptoms, such as fever, cough, and chest discomfort
- Itchy eyes or skin
- Organic dust toxic syndrome (“grain fever”)
- Rhinitis (a runny or stuffy nose)
- Skin rashes
Grain dust has long been associated with various diseases, including respiratory ailments and inflammatory conditions. The adverse effects of grain dust exposure are well-documented, yet it is still widely considered a “nuisance dust,” rather than a serious threat to worker health and safety.
Safety Standards & Regulations
To help combat the risks to agricultural and industrial workers, various entities, like the Occupational Safety and Health Administration (OSHA) and the National Fire Protection Association (NFPA) have implemented a series of safety regulations specific to the grain industry. These regulations are designed to prevent catastrophic explosions and long-term health issues associated with grain dust exposure.
Under OSHA’s 29 CFR 1910.272, employers are required to implement measures that control grain dust accumulation and eliminate ignition sources.
Key provisions include:
- Dust Accumulation Limits: Employers must initiate action to remove grain dust accumulations exceeding 1/8 inch in priority areas.
- Ignition Source Control: The use of compressed air for cleaning is permitted only when all machinery that presents a source of ignition in the area is shut down, and all other known potential ignition sources are removed or controlled.
- Emergency Preparedness: Facilities must develop and implement emergency action plans, including procedures for evacuation and employee training.
OSHA also addresses the health risks associated with grain dust exposure. The agency has established a permissible exposure limit (PEL) of 10 mg/m³ for total grain dust. However, studies have shown that respiratory symptoms can occur at levels between 10 and 15 mg/m³, indicating a significant risk even at concentrations below the allowable limit.
Additionally, the NFPA provides comprehensive guidelines for the prevention of fires and dust explosions in agricultural and food processing facilities.
NFPA 61 outlines best practices for:
- Facility Design: Recommendations for building layouts that minimize dust accumulation and facilitate cleaning.
- Dust Control Systems: Guidance on the installation and maintenance of dust collection and ventilation systems.
- Equipment Maintenance: Protocols for regular inspection and servicing of machinery to prevent overheating and friction, which can ignite dust.
Unfortunately, many employers fail to follow these and other safety standards. Dust explosions happen every single year in the United States, leading to dozens of injuries, multiple deaths, and millions of dollars in damage. When employers, manufacturers, and other major players fail to prioritize the safety of their workers, they must be held accountable. No matter what.
What to Do After a Grain Dust Explosion
It goes without saying that grain dust explosions are devastating. Victims and their families are typically left to pick up the pieces of their lives, while negligent companies are given fines that, more often than not, amount to little more than a slap on the wrist. Those who have been affected, whether they were injured while working at a grain processing facility or lost someone they loved due to a catastrophic explosion, should not have to shoulder the burden alone.
Grain dust explosions are almost never freak accidents. They often stem from serious safety violations, ignored warnings, or non-compliance with federal and state regulations. But, even if a settlement is offered, victims should avoid accepting a payout without first talking to a lawyer. Those responsible are eager to avoid paying victims and surviving family members what they are rightfully due. But working with an attorney can help you not only recover the full, fair compensation you are owed but also provide a sense of justice and closure that allows you to move forward.
- Categories