What to Know About Plant "Turnarounds"
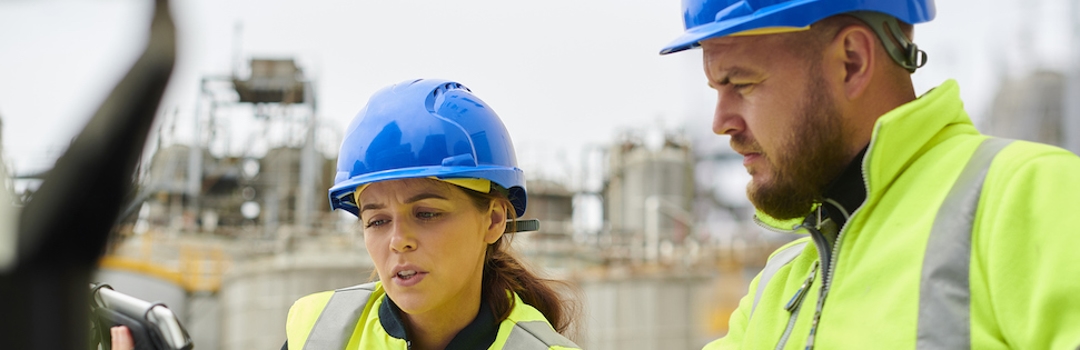
In this age of reliance upon oil and gas, oil refineries play an important role in keeping society up and running. But what happens when a refinery needs an update, or something goes wrong with a part of the facility?
To help ensure refineries stay in the best possible condition, they must undergo regular maintenance procedures called turnarounds.
As necessary as they are, turnarounds can pose serious risk to the workers operating a refinery or plant. In fact, considering how long in advance a refinery should start to prepare for a turnaround, hundreds of contractors can be involved in a single event, which only increases costs and risks.
What Is a Turnaround?
A turnaround, sometimes called a TAR, is a regular, planned procedure that takes part or all of an oil refinery (or other industrial plants) offline to allow personnel to inspect and renovate the facilities. Turnarounds can be incredibly expensive, sometimes contributing to a significant portion of a refinery’s annual budget.
Turnarounds are typically scheduled in the spring or fall, both of which are transitional seasons. Because these processes are intense, they are difficult to do in the extreme temperatures of winter and summer. That’s why they’re planned when production is slowest so as not to disrupt operations during peak seasons.
How Long Does a Refinery Turnaround Last?
A typical turnaround can last anywhere from a few weeks to a few months; major turnarounds can last years. The length of time depends entirely on the scope of work as well as how smoothly the process goes. Smaller procedures can happen twice a year, while major turnarounds tend to occur every 3-5 years. Because turnarounds are so expensive, and because having refineries shut down can dramatically impact the price of gas and other resources, oil rig companies may think it’s in their best interest to speed up the turnaround process—or skip it altogether.
However, the more rushed a turnaround is, the more likely it is to endanger workers. If oil companies try to hurry through turnarounds, something important could be missed or safety procedures could be overlooked.
What Is the Difference Between a Turnaround and a Shutdown?
On the surface, the main difference between turnarounds and shutdowns is that turnarounds are scheduled while shutdowns occur in response to circumstances such as a lack of supplies, accidents, or natural disasters.
But there’s another type of interruption that is less often mentioned: outages. These are different from turnarounds and shutdowns in that they don’t happen to protect equipment or people; instead, they happen because power is interrupted or equipment breaks down. Because outages are harder to plan for, they can be just as dangerous.
What Are the Five Phases of a Plant Turnaround?
The five phases of a turnaround are defined as follows:
- Scoping. Throughout this phase, the initial planning is done and important aspects like timeframe, budget, and which parts of the plant need to be addressed are decided.
- Preparation. Considering the big-picture planning that was completed during the scoping phase, detailed planning will be carried out by various specialty workers. This phase requires a lot of moving parts and can take anywhere from 6-18 months.
- Execution. As soon as the plant shuts down for the turnaround, the execution phase begins. Contractors will carry out work orders and test each asset for successful operation. Although this is often the shortest phase up until this point, lasting between 1-14 days, it can also be the most hectic and dangerous.
- Start-up. Before the plant is started up after the turnaround, a final inspection will occur. During this phase, the new procedures laid in previous stages are run for the first time. Because there is often pressure to complete this phase as quickly as possible, data is often left unverified, which can pose serious safety risks to the workers as well as the communities surrounding the plant.
- Review. Within two weeks of turnaround completion, a review phase may be conducted in order to determine how to improve the process in the future or to fill in any gaps in the work left undone.
What Are the Risks of Turnarounds?
Thousands of workers are involved in the turnaround process, which is one of the most intense and stressful parts of industrial work. Because of the nature of turnarounds, they can be incredibly dangerous if performed by untrained personnel or without the proper personal protective equipment (PPE). Companies must be held responsible for maintaining a safe workplace; when they don’t, workers can get seriously injured or even lose their lives.
The hazards of refinery turnarounds include:
- Exposure to toxic chemicals
- Improper storage of materials
- Fire and explosions
- Collisions of heavy equipment
- Slips and falls
While these dangers are present during a refinery’s normal operation, they are dramatically increased when a turnaround is in progress. In fact, while a refinery only operates in turnaround startup and shutdown modes 5% of the time, these periods are responsible for 40% of risk-related incidents.
Should there be a roadblock at any point during a turnaround, the timeline, costs, and risks associated will be affected. For this reason, it is of utmost importance that oil companies take care to employ safety measures throughout the process. When the companies refuse to put people before profits, the plant accident attorneys at Arnold & Itkin will be there to hold them accountable. No matter what.
- Categories