Chlorine Gas Hazards & the New Mexico Cheese Factory Spill
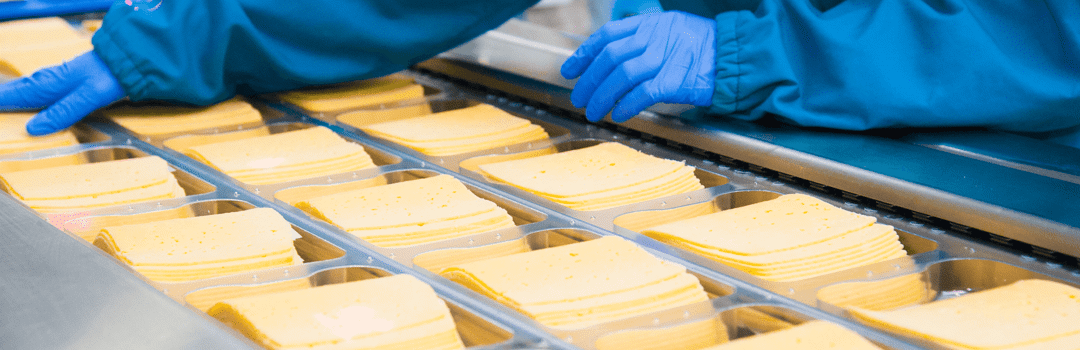
Just after 9:00 a.m. on December 20, 2024, emergency personnel with the Curry County Sheriff's Office and Clovis Fire Department responded to a call regarding a toxic leak at the Southwest Cheese factory just south of Clovis, New Mexico. Equipment at the cheese plant had malfunctioned and spilled 8.67 gallons of acid that mixed with 0.61 gallons of chlorine, creating a toxic gas.
At least 20 factory workers were injured after being exposed to the gas, with 14 taken to local hospitals. Two were critically injured.
At a factory, refinery, or plant, a chemical spill of any size can have cataclysmic effects. The spill at Southwest Cheese was relatively small compared to other notable incidents—such as the 4,000-gallon PFAS spill at the Cannon U.S. Air Force Base in Clovis on August 14, 2024—but the effects were still significant.
Owners and operators of industrial sites must implement strict standards regarding the storage, handling, and disposal of these substances, not only in food production but also at any location where hazardous chemicals are present. Equipment must be properly inspected and maintained to avoid dangerous leaks. Comprehensive emergency response measures must be in place in the event of a spill.
Anything less puts workers and neighboring communities at risk.
About Southwest Cheese
Established in 2005, Southwest Cheese is a major player in dairy processing, producing more than 588 million pounds of block cheese annually, alongside whey protein ingredients. The plant processes vast quantities of milk into premium cheese products distributed nationally and globally. Employing hundreds of people from the Curry County area, Southwest Cheese significantly contributes to the local economy but also holds a considerable responsibility to maintain stringent safety standards.
Like many food production facilities, Southwest Cheese uses chemicals for sanitation purposes—specifically chlorine-based solutions—as well as various acids, including nitric and phosphoric acid. Chlorine is commonly employed for disinfecting surfaces and equipment, killing bacteria, and maintaining strict hygiene standards essential for food safety. Nitric acid may be used for cleaning and descaling equipment to prevent contamination and maintain the efficiency of machinery. Food-grade phosphoric acid may be used as a processing aid in food products, including cheese, to regulate pH levels, improve texture, and extend shelf life.
The Risky Combination: Chlorine & Acid
Chlorine and acid become extremely hazardous when combined. When mixed, they may produce chlorine gas—a highly toxic, corrosive, and potentially deadly chemical that was historically used in warfare. Exposure to even small amounts of chlorine gas can lead to severe respiratory distress and chemical burns to the eyes, skin, and lungs. It can be fatal in larger concentrations.
In addition to food processing plants like Southwest Cheese, various facilities present risks of chlorine gas exposure. Water treatment plants, pulp and paper manufacturers, chemical producers, and agricultural processing plants frequently handle chlorine and acids. Any lapse in safety protocols, equipment malfunctions, or improper storage can trigger similar dangerous incidents.
In October 2024, 7 people were hospitalized as the result of a chlorine gas leak at the Central Water Plant in Horseshoe Bay, TX. The incident occurred when a truck driver accidentally mixed two chemicals in a holding tank, causing a reaction that released chlorine gas into the air. Even though the tank was shut down within a few minutes, the gas that had already been released lingered in the air, exposing the driver and nearby workers—and prompting a shelter-in-place order for nearby residents.
Exposure to chlorine gas can also occur in non-industrial workplaces, with tragic results. In November 2019, a Buffalo Wild Wings manager died from exposure to chlorine gas after an employee inadvertently applied a chlorine-based cleaning solution over an area of the floor that already had an acid-based cleaning agent on it. When the employee started to scrub the floor, a chemical reaction occurred and chlorine gas was released into the air, quickly spreading through the restaurant.
Thirteen people, including 2 customers, were hospitalized. The manager attempted to collect and remove the liquid using a squeegee, but he was overcome. Though he managed to get out of the building, he later died at the hospital.
Health & Safety Hazards of Chlorine & Chlorine Gas
According to the Environmental Protection Agency (EPA), chlorine gas was first registered in the United States in 1948 as a disinfectant to be used in sewage systems, drinking water, cooling towers, and swimming pools. It was classified for general use in 1976 under the premise that industrial users were already trained in its application. The EPA’s Office of Water regulates chlorine gas in potable water systems, while the Food and Drug Administration (FDA) regulates its use in solutions for sanitizing food contact surfaces. The Occupational Safety and Health Administration (OSHA) also enforces limits on workplace chlorine exposure.
At room temperature, chlorine is a yellow-green gas with a pungent, bleach-like odor. It is typically stored as a gas in large tanks or smaller cylinders. When dissolved in water, chlorine helps eliminate bacteria, algae, and other contaminants. Thanks to its powerful disinfecting properties, chlorine is a mainstay in food processing environments, chemical production, and water treatment facilities. Although indispensable for many industrial processes, chlorine can become dangerous or even deadly when not properly contained or monitored.
Exposure to chlorine gas can cause:
- Respiratory Irritation: Mild contact can lead to coughing or shortness of breath, but higher concentrations damage lung tissue and can be fatal.
- Skin & Eye Burns: Chlorine’s corrosive nature causes chemical burns to exposed skin and serious eye injuries.
- Long-Term Health Issues: Chronic exposure may exacerbate asthma or other respiratory conditions.
Chlorine itself is not flammable, but it intensifies fires when combined with certain chemicals or combustible materials. Improperly stored chlorine cylinders or tank leaks also risk explosion if container integrity is compromised.
Keeping Workers Safe Around Chlorine & Acid
Chlorine gas and chlorine mixtures can be equally devastating, leading to forced evacuations, medical emergencies, and sometimes long-term shutdowns of entire worksites. For companies using chlorine, worker safety must remain a top priority.
Employers can prevent chlorine hazards in various ways:
- Engineering Controls: Closed systems, automatic shutoff valves, and robust ventilation can prevent chlorine gas leaks.
- Proper Storage & Labeling: Chlorine cylinders and tanks need clear identification, secure valves, and well-ventilated storage.
- Regular Maintenance & Inspections: Equipment failures often spark chlorine-related emergencies. Scheduled checks reduce the risk of leaks or malfunctions.
- Protective Gear & Training: Employees should wear chemical-resistant gloves, goggles, and respiratory protection while handling chlorine. Thorough onboarding and regular safety drills ensure rapid, competent response to potential leaks.
- Emergency Response Plans: Worksites should have clear evacuation routes and communication protocols if chlorine is released to minimize after-effects.
Chlorine has numerous uses across many industries, but it must be managed properly to ensure the well-being of workers everywhere. That responsibility lies on employers, site managers, property owners, and other companies involved in its storage and use. For the workers at Southwest Cheese or any industrial site where chlorine poses a risk, that responsibility means everything. Because, in the end, it is workers who will pay the price for safety lapses.
- Categories