Job Safety Analysis (JSA) & Other Risk Assessments in the Workplace
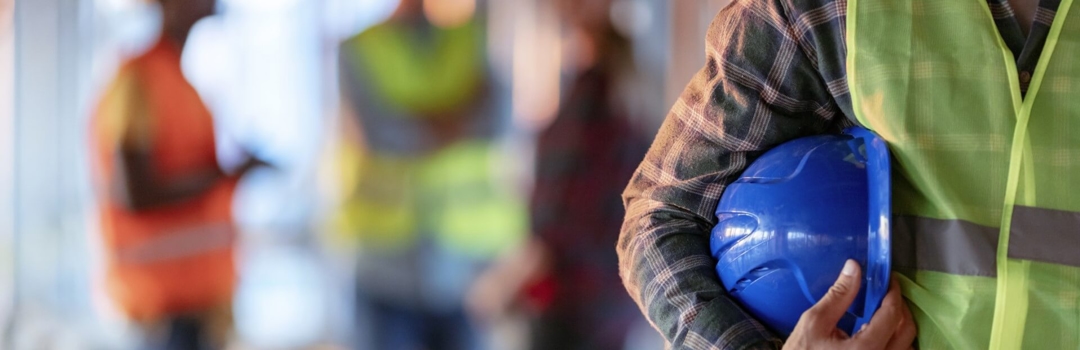
Whether you work in an industrial factory, on an offshore vessel, or on the road as a long-distance trucker, there are risks associated with your everyday tasks on the job. You have the right to be protected against these risks, and your employer is responsible to ensure that right is upheld. One of the ways that a company can be compliant with OSHA regulations is by implementing a job hazard assessment (JHA), also known as a job hazard breakdown or a job safety analysis (JSA).
What Is a Job Safety Analysis?
A job safety analysis is a procedure conducted to assess the risks associated with a particular task or job, and to integrate the accepted safety and health principles set by institutions like OSHA. Due to changing regulations, updated equipment, and other factors, it’s important to update this analysis regularly.
A JSA, and especially a written, distributed procedure based on the analysis, can serve as the basis for regular contact between an employer and an employee. More importantly, however, it can also prevent dangerous accidents as a part of initial training or briefing for infrequent jobs.
In some cases, an employer may choose to expand their job safety analysis to include all aspects of the job, which addresses the idea that safety is an important part of every task. When the scope is increased like this, the procedure is referred to as total job analysis.
What Are the 4 Steps of a Job Safety Analysis?
Regardless of whether the job is routine or non-routine, a JSA can (and should) be performed. Even a single task job should be analyzed for safety.
The four steps of completing a job safety analysis (JSA) are:
- Select the job to be analyzed. This process should be completed for every job on a work site, no matter how small or simple. Often, to address practical constraints of this implementation, an employer should assess the most critical jobs first.
- Break the job down into a clearly defined sequence. Risk can only be assessed with a full understanding of the job being analyzed. Defining the steps of a job can not only help determine the dangers associated with it, but it can also more clearly prepare the workers performing the tasks to complete the steps properly.
- Identify the potential hazards associated with each task in the job. It’s important to develop the list of hazards in the order that they are encountered by workers performing the job. Additionally, the workers themselves should be consulted for insight.
- Develop preventative measures to protect workers from hazards. This step can be further broken down into four common strategies:
- Eliminate the hazard
- Contain the hazard
- Revise the work procedures to reduce risk
- Reduce hazard exposure
Can JSAs Make a Workplace Safer?
Because a JSA’s main purpose is to define the safest way to complete a task or a series of tasks, it is an integral part of maintaining a safe working environment. By identifying potential hazards before they occur, employers can take proactive measures to protect their workers, which can significantly reduce the number of workplace injuries and accidents.
Practical Applications of JSAs in Various Industries
In the construction industry, where workers are frequently exposed to dangerous machinery, heights, and hazardous materials, JSAs can pinpoint specific risks associated with each task, such as operating a crane or working on scaffolding. By outlining clear safety protocols, construction companies can prevent accidents and ensure compliance with OSHA standards.
Manufacturing environments often involve complex machinery and repetitive tasks. A JSA can help identify risks such as machine malfunctions, ergonomic hazards, and chemical exposures. Implementing preventive measures like proper machine maintenance and employee training can mitigate these risks.
Healthcare workers face unique challenges, including exposure to infectious diseases, handling hazardous medications, and managing patient-related injuries. Conducting JSAs can help healthcare facilities develop safety protocols for tasks like patient lifting and administering treatments, reducing the risk of injury and improving overall patient care.
Long-distance truckers and other transportation workers are at risk of fatigue-related accidents, vehicle malfunctions, and cargo handling injuries. A JSA can address these risks by establishing guidelines for rest breaks, vehicle inspections, and proper loading techniques, enhancing safety on the road.
Benefits of Implementing Job Safety Analyses
- Increased Awareness: JSAs foster a culture of safety by raising awareness of potential hazards among employees. When workers are actively involved in the safety analysis process, they become more conscious of their actions and the associated risks.
- Improved Communication: Regularly updating and discussing JSAs encourages open communication between employers and employees. This ongoing dialogue helps identify new hazards and ensures that everyone is on the same page regarding safety procedures.
- Regulatory Compliance: Adhering to OSHA regulations and other safety standards is crucial for avoiding fines and legal issues. Conducting JSAs ensures that a company remains compliant with these regulations, protecting both the business and its workers.
- Reduced Costs: Workplace accidents can result in significant financial losses due to medical expenses, workers' compensation claims, and lost productivity. By preventing accidents through JSAs, companies can save money and maintain a more efficient operation.
Since the introduction of JSAs and OSHA regulations, worker deaths have decreased significantly. In 1970, the United States lost nearly 38 workers every day, compared to 15 daily in 2019. Worker injuries and illnesses have also decreased from 10.9 incidents per 100 workers in 1972 to 2.9 incidents per 100 workers in 2019.
Studies indicate that when workers perceive safety risks, their adherence to safety codes and ability to detect risks improve significantly. This heightened awareness contributes to safer work practices and environments.
Other Types of Risk Management
What is the William Fine Method?
The William Fine Method is a risk assessment tool used to evaluate the potential hazards in various industrial settings, prioritize them, and recommend appropriate corrective actions. This method is particularly useful in industries with complex processes and significant safety risks, such as the automotive, oil and gas, and manufacturing sectors.
The William Fine Method is not specifically a type of job safety analysis, but it can be considered a complementary tool within the broader framework of hazard assessment and risk management, which are integral parts of JSA.
While a JSA focuses on identifying hazards and determining safety measures for specific job tasks, the William Fine Method can be used to further assess and prioritize these hazards. Here's how they can work together:
- Hazard Identification: In the JSA process, hazards are identified for each step of a job task.
- Detailed Risk Assessment: The William Fine Method can be applied to these identified hazards to quantify the risk levels.
- Prioritization and Action: Based on the risk scores from the William Fine Method, the most critical hazards can be prioritized for immediate corrective actions.
What Is FMEA?
Failure Modes and Effects Analysis (FMEA) was first developed in the 1940s by the U.S. military as a systematic method for identifying potential failures in a design, manufacturing, or assembly process. This method has since become a fundamental process analysis tool used across various industries.
FMEA is a step-by-step approach for identifying all possible failures in a system, process, product, or service. Its primary goals are to:
- Identify Failure Modes: Determine all the ways, or modes, in which a system might fail. These failures are any errors or defects, especially those affecting the customer.
- Analyze Effects: Study the consequences of these failures to understand their impact.
- Prioritize Failures: Rank failures based on the severity of their consequences, frequency of occurrence, and ease of detection.
- Eliminate or Reduce Failures: Take actions to eliminate or reduce failures, starting with the highest-priority ones.
While FMEA is not a type of JSA, they can complement each other in creating a comprehensive safety program:
- Integration: An organization might use JSA to identify hazards in specific job tasks and then apply FMEA to analyze the potential failure modes of equipment or processes used in those tasks.
- Depth of Analysis: JSA provides a task-level analysis of hazards, whereas FMEA offers a more in-depth analysis of failure modes and their systemic impacts. Together, they provide a holistic view of safety and reliability.
- Preventive Measures: Both methods aim to prevent accidents and failures, but JSA focuses on immediate job-specific hazards, while FMEA addresses potential failures in the broader system or process design.
Protecting Workers From Risks On the Job
Maintaining a safe workplace is crucial. Each work environment presents unique risks, but the responsibility to protect workers from these risks remains universal. Implementing a JSA is a fundamental way for companies to comply with OSHA regulations and uphold their duty to ensure worker safety.
By proactively identifying and addressing hazards through JSAs and complementary risk management methods, companies demonstrate their commitment to protecting their employees. This not only ensures compliance with safety regulations but also fosters a culture of safety that benefits everyone. By prioritizing safety, employers can create a more productive, efficient, and harmonious work environment, ultimately leading to the well-being and satisfaction of their workforce.