Machine Guarding Hazards: Risks for Agricultural, Maritime & Construction Workers
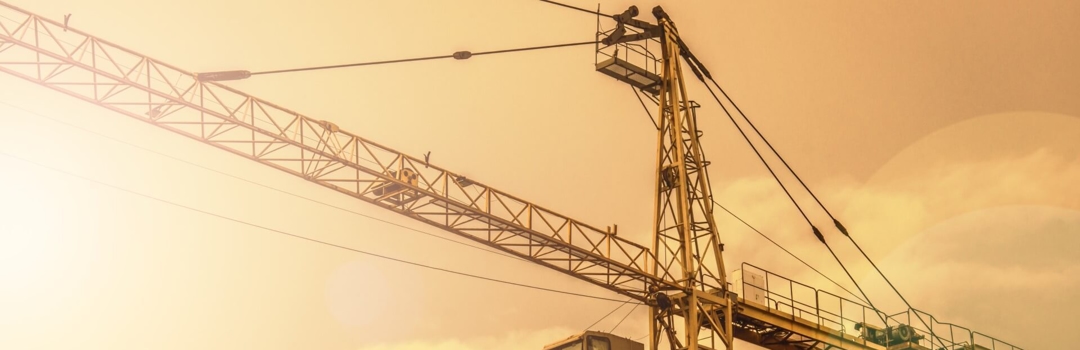
In industries like agriculture, maritime, and construction, machines are integral for driving productivity and efficiency. However, these powerful machines also introduce significant risks to workers, particularly when machine guarding is inadequate or ineffective. From crushed fingers and amputations to serious burns and blindness, the injuries resulting from poorly guarded machinery are often severe and life-altering.
Unfortunately, improper machine guarding is an all-too-common problem. According to the Occupational Safety and Health Administration (OSHA), machine-related accidents contribute to approximately 18,000 occupational injuries—such as amputations, crush injuries, and lacerations—each year, as well as more than 800 deaths.
OSHA Machine Guarding Standards: More Than a Suggestion
The Occupational Safety and Health Administration (OSHA) addresses machine guarding hazards in specific standards for agriculture, maritime, and construction. OSHA's regulations, such as 29 CFR 1910.212 for general industry and similar provisions for maritime and construction, provide a framework to safeguard workers from machine-related hazards.
Key areas covered by OSHA include:
- Types of Guards: Barrier guards, two-hand tripping devices, and electronic safety devices are some methods of protecting workers from dangers like nip points, rotating parts, and flying debris.
- Point of Operation Guarding: This is critical in preventing contact with dangerous parts of machinery where work is performed. For example, machinery like guillotine cutters, power presses, and milling machines require strict guarding measures.
OSHA’s safety regulations are not just suggestions; they are requirements that all employers and worksites must follow. Failure to abide by these and other OSHA standards results in thousands of injuries and deaths, as well as millions of dollars in fines, every year in the United States.
The Dangers of Ineffective Machine Guarding
Ineffective machine guarding is a critical issue in any sector, but particularly in industries like agriculture, maritime, and construction, where the use of dangerous machinery is common. When machine guards are poorly designed, improperly installed, or inadequately maintained, they can fail to protect workers from hazardous machine parts.
For example, imagine a worker at a busy construction site is tasked with operating a heavy-duty machine designed to lift and move large steel beams. The machine’s protective guard has been removed for maintenance and is never replaced, leaving the gears and moving parts exposed. As the worker maneuvers the machine, their glove gets caught in the unguarded mechanism. In an instant, their hand is pulled into the gears, resulting in a severe injury that requires multiple surgeries and months of recovery.
Avoidable accidents like these highlight the very real—and very deadly—risk of improper machine guarding. In industries like construction, agriculture, and maritime, such lapses can lead to amputations, crush injuries, or even fatalities. Workers who depend on proper safety measures often pay the price for employer negligence, costing them their health, their livelihoods, and, sometimes, their lives.
Improper machine guarding can take many forms, such as:
- Guards that do not fully cover dangerous parts of the machine, such as rotating shafts or cutting blades, leave workers exposed to serious risks. Even small openings in guards can allow for accidental contact, leading to injuries.
- Guards that are not securely fastened or are made from weak materials can be easily bypassed or damaged during normal operations. This can lead to situations where guards are removed or fail during use, exposing workers to hazardous parts.
- Guards that are designed or installed in ways that interfere with machine operation, which can prompt workers to bypass or remove them, putting them at risk of serious accidents and injuries.
- Industrial machinery is subject to wear and tear, and guards are no exception. Without regular inspection and maintenance, guards can become damaged or dislodged, reducing their effectiveness.
The Importance of Hazard Recognition
Recognizing the hazards associated with machinery requires a thorough understanding of how these machines operate, as well as the specific risks they present. OSHA provides guidelines, checklists, and training materials to help workers and employers identify and mitigate these hazards.
Some key aspects of hazard recognition include:
- Understanding Machine Operations: Workers need to be trained on how each machine functions, including identifying potential pinch points, rotating parts, and other dangerous areas.
- Regular Inspections: Machines should be inspected and maintained regularly to ensure guards are in place and functioning correctly.
- Awareness of High-Risk Activities: Activities such as clearing jams, adjusting machinery, or performing maintenance without proper safety protocols are particularly hazardous.
Employers MUST provide workers with adequate information and training to ensure their safety on the job. Failure to do so constitutes negligence and can have devastating consequences.
Machine Guarding Challenges in Agriculture
Agricultural workers often use a variety of large, powerful machines, such as tractors, harvesters, and grinders. These machines have numerous moving parts, creating pinch points and other hazards that can lead to severe, even life-threatening injuries. For example, the point of operation on a harvesting machine can easily cause amputations if proper guarding is not in place.
Tractors & Their Potential Hazards
Tractors are a staple of agricultural work, used for plowing, planting, and towing heavy equipment. However, tractors are also one of the leading causes of fatalities and severe injuries in agriculture.
The main dangers associated with tractors include:
- Rollovers: Tractors can overturn, especially on uneven terrain, leading to crush injuries or death.
- Power Take-Off (PTO) Shafts: PTO shafts transfer power from the tractor to attached equipment. Exposed PTO shafts can entangle clothing or limbs, causing amputations or other severe injuries.
- Pinch Points and Crush Zones: Tractors have numerous moving parts, including hydraulic systems and hitch points, where workers can be caught or crushed.
Harvesting Machine Risks & Concerns
Harvesters, including combine harvesters and cotton pickers, are critical for gathering crops efficiently. However, these machines also have several hazardous components.
These include:
- Cutting Blades: Harvesters use sharp blades to cut through crops, and these blades can cause severe lacerations or amputations if not properly guarded.
- Conveyor Belts and Augers: These components move crops through the machine. Workers can be caught in these moving parts, leading to serious injuries.
- In-Running Nip Points: Harvesters have numerous nip points where moving parts come together, creating a high risk of entanglement.
Grinders & Choppers: Common Safety Issues
Grinders and choppers are used to process crops into smaller pieces, whether for feed, compost, or other purposes.
These machines pose significant dangers due to their high-speed rotating blades, including:
- Cutting and Shearing Hazards: The primary risk with grinders and choppers is the cutting and shearing action of the blades. Without proper guarding, workers can suffer severe lacerations or amputations.
- Thrown Objects: If a grinder or chopper malfunctions, it can throw objects at high speed, posing a risk of blunt force injuries.
Maritime Machine Guarding Challenges
The maritime industry presents unique challenges for machine guarding due to the often-confined spaces in which these machines operate, as well as the variety of equipment used. Workers may operate cranes, conveyors, winches, and other heavy equipment, all of which have moving parts that can cause injuries.
Some key machine guarding safety concerns in the maritime industry include:
- Crane Accidents: Cranes are indispensable for lifting and moving heavy loads on ships and at docks, but they also introduce several hazards, including falling loads; crush and pinch points caused by the movement of booms, hooks, and cables; and the swing radius of the crane, especially in confined spaces.
- Winch Accidents: Winches, used to wind and unwind cables or ropes for lifting, pulling, or securing loads on ships, also present significant hazards such as rotating drums, high-tension cables, and pinch points. Ineffective guarding on these tools can lead to serious injuries caused by recoil or requiring amputation.
- Machine Entanglement: Conveyors are frequently used in maritime settings to move materials like cargo, coal, and grain. However, they present several dangers. Loose clothing or personal protective equipment (PPE) can easily become entangled in moving conveyor parts, pulling workers into the machinery. Similarly, nip points can occur where belts or chains move around pulleys, causing workers’ hands, clothing, or tools to become trapped. If not properly guarded, these can lead to severe injuries or amputations.
- Unexpected Machine Movement: Hydraulic systems are essential for operating cranes, winches, and various ship equipment. Proper guarding and regular maintenance are essential to prevent the dangers of high-pressure leaks as well as crush injuries caused by the unexpected movement of heavy machinery.
The variety of machinery used in the maritime industry requires diligent attention to machine guarding. Ineffective guarding or a lack of adherence to safety standards can turn routine operations into life-threatening situations. Employers, workers, and other parties MUST ensure that all machines are properly guarded. Additionally, workers must be adequately trained in the dangers and safety protocols associated with these machines.
Machine Guarding in Construction
The construction industry continues to be one of the most hazardous sectors for workers in the United States. This is partially due to the large amount and wide variety of heavy equipment and machines construction workers must use every single day. From power tools, like saws and drills, to heavy equipment, such as bulldozers, cranes, and excavators, these machines pose a wide range of risks—especially when guards are lacking.
Some of the most dangerous machines commonly used in the construction industry include:
- Power saws, including circular saws, table saws, and reciprocating saws, are among the most commonly used tools on construction sites. These machines have sharp, rotating blades that can cause severe injuries if they are not properly guarded. Drills, especially heavy-duty ones, also pose significant risks due to their high-speed rotating parts, which can catch clothing, hair, or fingers.
- Bulldozers and excavators are essential for tasks like earthmoving and demolition, but they present significant dangers due to their size and power. Moving parts, such as tracks, buckets, and blades, create pinch points and crush hazards. Ineffective guarding or improper maintenance of these machines can lead to catastrophic injuries and fatalities.
- Cranes are indispensable for lifting and moving heavy loads, but they also pose numerous hazards. The swing radius of a crane, combined with the potential for falling loads, creates significant risks. Workers and others in the vicinity of cranes can be struck by moving parts or crushed if proper safeguards and protocols are not followed.
- Concrete mixers and conveyors are commonly used to transport materials on construction sites. The rotating drums of mixers and the moving belts of conveyors can trap hands, fingers, or clothing, leading to serious injuries. Proper guarding is essential to prevent contact with these moving parts.
Beyond Machine Guarding: Proper Lockout/Tagout Programs
While physical machine guarding is essential for preventing accidents during regular operations, it is only one part of a comprehensive safety strategy. Equally important is the implementation of effective lockout/tagout (LOTO) programs, which protect workers during machine maintenance, servicing, and repair activities. In industries like agriculture, maritime, and construction, where machines are frequently serviced and maintained, lockout/tagout procedures are vital for preventing catastrophic injuries and fatalities.
What Is Lockout/Tagout?
Lockout/tagout is a safety procedure designed to ensure that machinery is completely shut off and cannot be restarted during maintenance or repair activities. This process involves isolating the energy sources that power the machine, such as electrical, hydraulic, pneumatic, or mechanical systems, and locking them in the "off" position. Additionally, a tag is placed on the machine to alert others that it is being serviced and should not be operated.
LOTO programs are essential because they prevent the accidental or unauthorized re-energization of machines while workers are in potentially hazardous areas, such as inside the machine or near dangerous moving parts.
Protecting Workers with Proper Machine Guarding
Machine guarding is a critical aspect of workplace safety in agriculture, maritime, and construction. Adhering to OSHA standards, recognizing hazards, and implementing effective solutions, including lockout/tagout programs, can prevent severe injuries and save lives. Employers must prioritize machine guarding to protect their workers from the inherent dangers of operating and maintaining machinery in these industries.