The Hazards of Metal Fabrication: Why Metal Workers Face Greater Risks
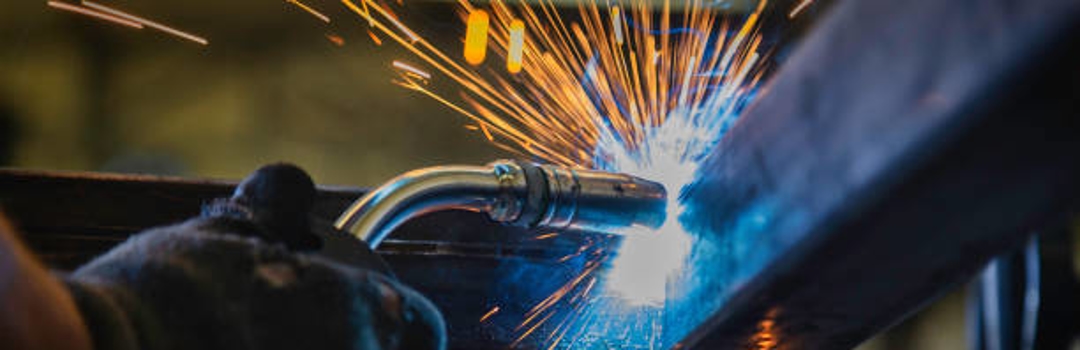
An iron plant in St. James Parish, Louisiana temporarily shut down when one of its workers died in an onsite accident; an El Paso, Texas metal fabricator was fined over $350,000 for numerous safety violations after a worker required treatment for second-degree burns, and a Dallas-based metal recycling company was cited for repeated health and safety violations when a worker was hospitalized after a stack of pipes fell and crushed him. These serious incidents represent just a small fraction of the many workplace injuries and deaths that occur each year in the metal fabrication industry.
According to data from the Occupational Safety and Health Administration (OSHA), more than 200 inspections conducted in the region spanning Louisiana, Texas, and New Mexico—including one stemming from a fatality—uncovered over 500 violations, resulting in penalties of more than $1.5 million. This data suggests that metal fabrication workers face a heightened risk of on-the-job injuries. Why is this the case?
Some of the risks are simply due to the intrinsically dangerous nature of the job. Metal workers are required to operate high-powered machinery, work with harmful materials, and navigate environments rife with potential hazards. However, employers must follow strict regulations to ensure the health and safety of their workers. Employer negligence in the form of safety violations can have devastating or even deadly consequences.
What Is Metal Fabrication?
Metal fabrication is a critical component of the larger economy. Essentially all metal products—from various forms of infrastructure, like metal bridges, to electronic components, appliances, and automotive parts—come from the metal fabrication industry.
In the U.S., metal fabrication comprises both the public and private sectors, with private companies making up the bulk of the industry. These entities employ millions of workers in a wide variety of capacities.
Some of the most common types of metalworking jobs include:
- Computerized numerical control (CNC) operators
- Engineers
- Fabrication technicians
- Fitters
- Line equipment operators
- Machine operators
- Mechanical engineers
- Metal fabricators
- Metalworking specialists
- Mold makers
- Plating technicians
- Robotic weld technicians
- Sheet metal foremen and mechanics
- Sheet metal installers
- Torch cutters
- Welders and precision welders
These and other metal workers are responsible for constructing, repairing, maintaining, and installing all types of metal goods, products, and parts. Depending on the employer and the job itself, workers may spend hours on their feet in manufacturing plants or small shops, operating heavy machinery, using high-powered tools, entering confined spaces, or working at great heights. It’s no surprise, therefore, that the risk of injury is high.
Common Risks in the Metalworking Industry
Workers in the metal fabrication industry face numerous risks every day on the job. As previously mentioned, they must operate heavy machinery and tools, work with hazardous materials and substances, and navigate confined spaces, heights, and other potentially dangerous situations. According to OSHA, data from the Bureau of Labor Statistics (BLS) suggests that fabricated metal industry workers experience more work-related injuries and illnesses than in all of private industry.
Exposure to Harmful Substances
Occupational exposure is one of the most common—and most serious—risks associated with metal fabrication. Metalworking fluids, welding fumes, noxious gases and vapors, and other harmful materials can cause an array of respiratory illnesses, skin conditions, and cancers.
Metal fabrication workers may be exposed to a variety of toxic substances, chemicals, and materials, including but not limited to:
To protect workers from potential harmful exposure, employers should provide them with adequate personal protective equipment (PPE), including proper respiratory protection. Additionally, employers should follow all applicable hazard communication standards and ensure sufficient training to help reduce the risk of exposure and related injuries.
Unguarded Machinery and Power Tools
Due to the nature of the job, metal workers are frequently required to operate heavy machinery and power tools. To help reduce the risk of injury and death, employers are required to ensure proper machine guarding. Under OSHA regulations, all machines that have the potential to harm workers must be fitted with the appropriate machine guards.
This includes:
- Fixed guards
- Adjustable guards
- Self-adjusting guards
- Interlocking guards
Additionally, employers must routinely inspect machines and machine guards to ensure that they are correctly fitted and working properly. Hazards, including non-working machine guards, should be clearly labeled, and workers should be trained in correct usage, lockout and tagout policies, PPE use, and emergency procedures.
Lockout and Tagout Hazards
Lockout and tagout are industry terms used to refer to the control of hazardous energy. Specifically, lockout and tagout policies come into play when a machine, tool, or piece of equipment unexpectedly turns on or otherwise releases hazardous energy while being serviced, inspected, repaired, or maintained.
Hazardous energy sources include:
- Chemical energy
- Electrical energy
- Hydraulic energy
- Mechanical energy
- Pneumatic energy
- Thermal energy
Lockout and tagout hazards often lead to serious or even fatal bodily injuries, such as amputations, fractures, traumatic brain injuries, electrical shock, and burns—but proper lockout/tagout procedures help protect workers from these effects.
Confined Spaces
Metal workers are often required to work in confined spaces, including permit-required confined spaces.
By nature, confined spaces pose numerous risks to those who enter. These include:
- Poor ventilation
- Restricted access
- Slow entry/exit in case of emergency
- Too much or too little oxygen
- Flammable or combustible atmosphere
- Dangerous gases
- Exposure to harmful or toxic substances
- Flooding
Working in a confined space can lead to respiratory illnesses, such as pneumonia, asthma, or even lung cancer. Workers are also at risk of traumatic accidents, such as fires, floods, and explosions. To make matters worse, confined spaces have limited access points, making them difficult to exit quickly and posing challenges for rescuers attempting to enter when an emergency strikes.
Occupational Noise
Manufacturing plants, metal fabrication workshops, and other industrial settings are prone to excessive noise levels. As a result, workers in these environments are susceptible to hearing damage due to occupational noise. To help combat this, employers are required to provide workers with proper ear protection and ensure that workers do not spend too much time in excessively noisy environments.
OSHA regulations permit workers to be exposed to up to 90 dBA (weighted decibels) for up to eight hours in a single workday. This is known as the “permissible exposure limit” (PEL). Workplaces that violate the PEL are subject to punitive measures, including fines.
Employer Negligence in Metalworking
Metalworking is, by nature, a dangerous occupation—but this doesn’t mean that workers must simply put up with job-related accidents, illnesses, and injuries. In fact, employers in the metal fabrication industry are held to strict regulatory standards to help reduce risks to employees. Unfortunately, these regulations are not always enough to keep workers safe.
Far too often, employers commit violations that put workers at risk. Some of the most common employer violations in this industry include:
- Improper machine guarding, including point-of-operation and abrasive wheel guarding
- Failure to control hazardous energy/poor lockout and tagout procedures
- Inadequate or improper hazard communication
- Insufficient training, including poor powered industrial truck training
- Failure to provide sufficient personal protective equipment (PPE)
- Permitting or mandating excessive exposure to loud noises
- Permit noncompliance, including permit-required confined spaces
- Insufficient fall protection
Such negligence can—and often does—lead to tragic consequences. When it does, employers must be held accountable.
- Categories