When Machines Turn Deadly: Equipment-Related Injuries & Fatalities in the Workplace
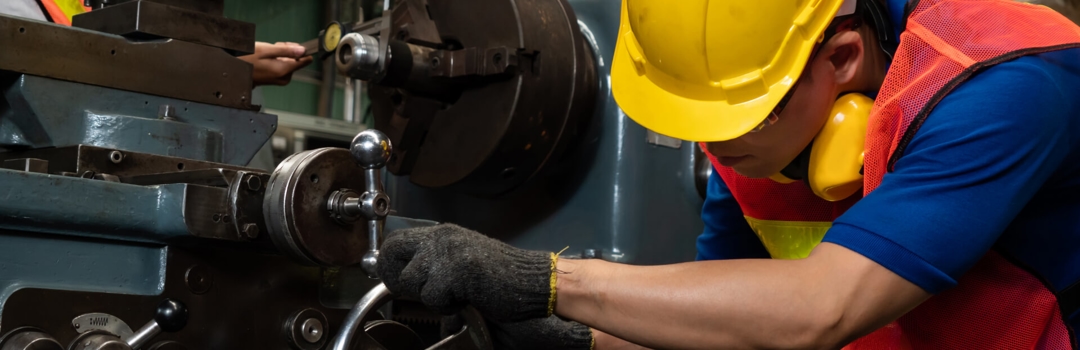
On June 19, 2024, a 44-year-old foreman was fatally electrocuted while carrying out storm recovery efforts in Coaling, Alabama. The worker, who was restoring distribution power to several natural gas pumps, came into contact with energized overhead power lines while replacing a broken switch. After suffering severe burns to his body, including his arms and face, the man died at the scene.
According to the Occupational Health and Safety Administration (OSHA), the foreman’s employer, Dexter Fortson Associates Inc., failed to meet basic safety standards, which included allowing the use of expired protective equipment and live-line tools. The contractor also failed to make sure that the equipment being used was de-energized, leading to the tragic incident. Dexter Fortson Associates Inc. was fined nearly $85,000 for these and other safety violations, but the family and loved ones of the killed worker are the ones who must shoulder the true cost of the company’s negligence.
Sadly, this is far from the only example of workers being injured or killed by unsafe, defective, or poorly maintained equipment. In fact, just days after the incident in Alabama, a 37-year-old worker at a Cleveland, Ohio bakeware manufacturing company suffered an amputation injury due to improperly secured pullbacks on a power press. Just two weeks later, a 64-year-old employee at the very same company sustained a similar amputation injury as a result of inadequate machine guarding and lock-out procedures on a mechanical power press.
How Common Are Work-Related Machinery & Equipment Accidents in the U.S.?
Every year, thousands of workers are injured or killed due to machinery- and equipment-related accidents. The National Safety Council reports that these types of incidents are the third-leading cause of occupational fatalities in the United States. From 2018 to 2022, almost 3,700 workers died as a result of contact with workplace equipment and objects, according to the Centers for Disease Control and Prevention (CDC). In 2022 alone, the CDC reports that more than 12% of all work-related fatalities were likely machinery related.
These incidents are not “accidents.” They are preventable tragedies that should never occur. When employers, manufacturers, and other parties ignore safety standards, cut corners, or fail to properly train employees on the proper use of machinery, they put their workers’ lives at risk.
Machines That Injure: A Closer Look at the Most Dangerous Workplace Equipment
Across every industry, workers rely on various tools and machines to do their jobs. But when that equipment malfunctions, is used improperly, or lacks essential safety features, the results can be catastrophic.
Here are some of the most common types of equipment involved in serious workplace injuries and fatalities across different industries.
Heavy Machinery & Industrial Equipment
Industrial settings, like plants and factories, are often filled with high-power machines capable of exerting massive forces. Without proper safeguards, these machines can quickly turn deadly.
Common industrial equipment risks include:
- Crushing and Entanglement Hazards: Rotating gears, exposed belts, and moving rollers can pull in clothing, hair, or limbs in seconds. Once entangled, a worker may have no time to react.
- Struck-By Incidents: Machinery arms, buckets, and suspended loads can swing unexpectedly, striking workers with fatal force.
- Tip-Overs and Rollovers: Some types of equipment, like loaders or excavators, are top-heavy and can easily tip or roll over, especially on uneven ground. These incidents often result in crushing injuries.
Some of the most dangerous types of industrial equipment include:
- Forklifts: Forklifts are one of the most dangerous pieces of equipment in the workplace. Improper turns, overloaded forks, or collisions can result in workers being crushed or run over.
- Conveyor Belts: A worker caught in a conveyor’s moving parts can suffer traumatic amputations or be pulled into the machinery. This can lead to catastrophic injuries and fatalities.
- Augers and Drills: Entanglement with an auger’s rotating shaft can lead to instant amputation or death. This is an especially high risk in agricultural and industrial settings where these machines are common.
- Press Machines: Metal presses and stamping machines exert immense force. In the absence of proper guarding or during maintenance without adequate lockout/tagout procedures, they can crush limbs or cause fatal injuries.
Construction Equipment
Construction zones are complex and dynamic environments filled with heavy machinery—and risk. According to OSHA and the Bureau of Labor Statistics (BLS), construction consistently rates among the most dangerous industries for workers. In 2021, almost 20% of all workplace fatalities occurred within the construction industry.
Some of the most common construction accidents include:
- Falls from Heights: Equipment like scaffolding and aerial lifts pose serious fall risks when safety rails or harnesses are missing or misused.
- Struck-By Accidents: Workers on foot are often injured by crane loads or excavator swings. These incidents frequently happen due to limited visibility or poor communication.
- Electrocution: Contact with overhead power lines during equipment operation is a major hazard, particularly with cranes and lifts.
These and other construction accidents are frequently connected to the use of various tools and machines, such as:
- Cranes: Defective or poorly maintained cranes can lead to load failures, tip-overs, and contact with electrical lines.
- Bulldozers and Excavators: Operators and nearby workers are at risk of being run over or pinned under machinery, especially during reversing or debris removal.
- Scaffolding and Aerial Lifts: Faulty setup, missing guardrails, or overloading can result in deadly falls and other incidents.
Agricultural & Farming Equipment
Farm work involves some of the most dangerous equipment, often in environments with limited safety oversight.
This can lead to machine-related accidents like:
- Entanglement in Moving Parts: Loose clothing or unguarded equipment like grain augers can pull workers into rotating shafts in an instant.
- Rollovers: Tractor rollovers are one of the leading causes of death in agriculture. Many fatalities occur when tractors tip on slopes or uneven terrain and lack rollover protective structures.
- Suffocation in Grain Bins or Silos: Workers can become engulfed in grain or trapped in grain bins or silos within seconds, leading to asphyxiation.
- Grain Dust Explosions: Faulty or poorly maintained equipment can heat up or spark, providing the necessary ignition source for catastrophic grain dust explosions.
- Amputation By Combines or Harvesters: These machines have fast-moving blades that can cause catastrophic injuries or death.
Warehouse & Transportation Equipment
In warehouses and distribution centers, the pace of work and volume of moving equipment amplify the risk of machine-related incidents. In fact, according to the BLS, transportation accidents are the leading cause of occupational fatalities in the U.S., making up 36.8% of all work-related deaths in 2023.
Common incidents include:
- Forklifts Accidents: Forklifts are responsible for about 87 fatalities and tens of thousands of injuries each year. Tip-overs, crush accidents, and struck-by incidents are the most common examples.
- Vehicle Collisions: Workers on foot can be hit by reversing trucks or forklifts due to blind spots or congested aisles in warehouses and other facilities.
- Falls from Heights: Falling from loading docks, semi-trailers, or even standing on elevated pallets can cause severe injury or death.
- Automated Guided Vehicle (AGV) Accidents: These robotic systems, commonly used in modern warehouses, can crush or pin workers if sensors malfunction or humans stray into their paths.
- Delivery Truck and Semi-Truck Crashes: Off-site accidents involving commercial vehicles often result in serious injuries and fatalities to truck drivers and others involved.
Oil, Gas & Mining Equipment
These high-hazard industries often require workers to deal with flammable materials, extreme pressure, and remote work sites, all of which increase the risk of injuries and fatalities.
Common hazards include:
- Explosions and Fires: Equipment failures, gas leaks, and electrical sparks can ignite large-scale explosions.
- Crushing Incidents: Workers can be pinned between moving equipment or crushed under shifting loads.
- Oil Rigs and Derricks: These environments are particularly hazardous due to high-pressure systems, complex machinery, and the remote nature of work.
- Mining Machinery: Equipment failures, cave-ins, and operator error contribute to a high rate of serious injuries.
- Gas Compressors and Pipelines: When these systems rupture or leak, the risk of explosion or asphyxiation is high.
Manufacturing & Processing Equipment
Factories and processing plants often involve repetitive, high-speed, high-force operations that can be extremely dangerous. When safety standards are ignored, the risks increase exponentially.
Examples of common machine-related incidents and injuries include:
- Caught-In and Crush Hazards: Assembly line machinery and rollers can trap body parts, especially when machine guards are removed or bypassed.
- Chemical Exposure: Processing equipment can release harmful fumes or gases, especially during cleaning or maintenance.
- Meat Processing Machines: Equipment like slicers and grinders are a leading cause of amputations in food manufacturing.
- Automated Robots: Manufacturing robots, if improperly programmed or maintained, can make unexpected movements and injure workers.
- Boilers and Pressure Vessels: When these systems rupture, they can explode with devastating force, resulting in burns or blunt trauma.
Electrical & Power Tools
Across nearly every industry, handheld tools can cause life-altering injuries or fatalities when they are defective, used incorrectly, or poorly maintained.
Examples of this include:
- Electrocution: Faulty wiring, improper grounding, or contact with live circuits are common in construction and industrial settings. This often occurs as a result of employers failing to implement or enforce safety standards, leading to tragic results.
- Explosions and Fires: Sparks from grinders, power saws, and other handheld tools can ignite airborne dust or vapor, leading to massive explosions, fires, and flash burns.
- Power Saws and Grinders: Power saws, grinders, and similar tools must have adequate safety guards, as kickbacks or blade malfunctions can cause severe lacerations or traumatic amputation.
- Drills and Nail Guns: Misfires or operator error can lead to eye injuries, puncture wounds, or even death. These tools must have adequate safety guards to protect workers who use them on the job.
- High-Voltage Equipment: Contact with energized transformers or panels can result in immediate electrocution, leading to severe injuries and death. This often occurs as a result of defective or outdated equipment.
Each of these examples represents more than just a set of statistics; they represent real workers, real lives, and, often, real consequences for families, loved ones, and entire communities.
Why Do Workplace Equipment Accidents Happen?
Workplace equipment injuries and fatalities don’t just happen—they are the result of specific, preventable failures. Behind every catastrophic incident is a series of decisions, oversights, and systemic issues that, when combined, create the perfect conditions for tragic workplace accidents. Whether it’s a forklift tipping over in a crowded warehouse or a worker caught in a moving auger on a farm, the root causes of these incidents are often all-too familiar.
Human Error or Lack of Training
Most equipment-related injuries are not the result of willful negligence but, rather, a lack of proper training. Workers are often placed on complex, high-powered machinery with minimal instruction beyond “get the job done.” Sadly, inadequate employee training or oversight can—and often does—have devastating consequences.
For example, a new warehouse employee might not understand the blind spots of a forklift. A temporary worker may not know the dangers of clearing a jam in a running conveyor. A contractor on a construction site might assume someone else has verified that power lines are de-energized. These are not hypothetical examples; they reflect the day-to-day reality in thousands of workplaces across the country. And, when training is rushed or inconsistent, the margin for error vanishes.
OSHA has repeatedly emphasized that comprehensive training is one of the most effective tools for preventing serious injuries. Yet, in high-turnover industries like construction, warehousing, and agriculture, training is often treated as a checkbox rather than a true investment in safety.
Lack of Machine Safeguards or Maintenance
Even the most cautious workers can’t protect themselves from a machine that’s been poorly maintained or stripped of safety features. In some cases, machine guards are removed to “make the job easier.” In others, emergency stop mechanisms are broken or, worse, never installed. Many machines carry warning labels and safety instructions that are faded, missing, or ignored, and worn parts often go unreplaced as employers try to cut maintenance costs.
But machine maintenance isn’t just about performance. It’s a cornerstone of safety. Many machinery-related injuries and fatalities involve equipment that was not functioning properly at the time of the incident. Employers have a legal obligation to ensure that all equipment is regularly inspected and properly guarded. When that responsibility is neglected, the consequences fall squarely on the workers—often with irreversible outcomes.
Improper Equipment Use or Overload
Heavy machinery is designed to do specific tasks under specific conditions. But in many workplaces, equipment is pushed far beyond its safe operating limits. Forklifts are overloaded, causing tip-overs that crush operators, or scissor lifts are used on unstable terrain or in high winds. In agriculture, tractors are operated without counterweights or on slopes beyond safe angles. Even handheld tools, like nail guns and grinders, may be used for jobs they weren’t designed to handle.
Sometimes, equipment is misused unintentionally. This is often the result of insufficient employee training or supervision. Other times, machine misuse is the result of a "make it work" culture that prioritizes output over safety. Either way, equipment operated outside its intended parameters becomes unpredictable and dangerous.
Absence of Lockout/Tagout (LOTO) Protocols
Maintenance and cleaning tasks are some of the most dangerous times to interact with machinery. That’s why OSHA requires lockout/tagout procedures—systems that ensure machines are completely de-energized before servicing. But far too often, LOTO procedures are skipped for the sake of speed or convenience.
The results can be devastating. Hands and arms caught in gears. Electric shocks. Crushing injuries from machinery that reactivates unexpectedly. LOTO isn’t just a bureaucratic formality; it’s a proven life-saving protocol. Its absence is a red flag for systemic safety failures, and employers who fail to implement it can and should be held accountable.
Pressure to Speed Up Production
Perhaps the most overlooked cause of workplace tragedies is also one of the most pervasive: the relentless pressure to meet deadlines and quotas.
This can look like a lot of things:
- Supervisors rushing workers through safety checks
- Operators being told to “skip the lockout” to avoid downtime
- New hires being put on equipment before they’re properly trained because “we’re short-staffed.”
- Maintenance getting delayed because the machine “can’t be taken offline right now.”
When production becomes the only priority, safety is the first casualty. This pressure is especially dangerous in high-risk industries where the line between routine and deadly is razor thin. It can lead otherwise careful, competent workers to take risks they would never consider under normal circumstances.
No job is worth a life. Yet, countless workplace deaths occur each year because someone, somewhere in the chain of command, prioritized output over human safety. These tragedies don’t occur in a vacuum. They are the product of choices, some made by individuals, but many made at the organizational or systemic level. Identifying and addressing these root causes is critical for preventing future injuries and holding the appropriate parties accountable when lives are shattered.
Preventing the Preventable: Safety Measures That Save Lives
Preventing workplace equipment injuries and fatalities isn’t just possible, it’s expected. The law requires it, technology supports it, and history has shown, time and again, that effective safety measures can drastically reduce the risk of serious workplace accidents.
Machine Guarding
Machine guarding is one of the simplest, most effective ways to prevent entanglement and crush injuries. These barriers physically block access to dangerous parts of machinery, such as belts, gears, augers, and rollers.
OSHA’s general requirements for all machines (Standard 1910.212) requires that machinery be equipped with guards that eliminate the risk of accidental contact with moving parts. When guards are removed, bypassed, or never installed, workers are exposed to lethal hazards, often with little warning.
Lockout/Tagout (LOTO) Procedures
LOTO protocols ensure that machinery is completely shut down and cannot be restarted while maintenance is underway. It’s a vital safeguard against electrocution, crush injuries, amputation, and other catastrophic injuries. OSHA provides specific standards for lockout/tagout practices, but employers do not always follow or enforce them.
Lack of proper LOTO procedures is a direct factor in numerous documented workplace fatalities, including incidents where machines restarted while a worker was inside or under the equipment. Despite its importance, however, many workplaces still view LOTO as optional. Sadly, this can be a deadly misconception.
Personal Protective Equipment (PPE)
While not a substitute for engineering controls, personal protective equipment, or PPE, is a critical last line of defense. PPE includes anything workers wear to protect against possible injuries, such as construction helmets, cut-resistant gloves, or flame-resistant clothing. PPE must be properly fitted, maintained, and matched to the hazard. Too often, workers are given inadequate gear—or none at all—especially in lower-wage or temporary roles.
Training & Safety Protocols
Training isn’t just about knowing how to turn a machine on. It’s about understanding risks, recognizing hazards, and knowing how to respond in an emergency.
Effective employee training programs include (but are not limited to):
- Forklift operator certification
- Site-specific hazard orientation
- Training on the unique risks of augers, cranes, aerial lifts, etc.
- Hands-on instruction, not just checklists or online modules
Well-trained employees are empowered to spot unsafe conditions, report issues, and avoid hazardous shortcuts. This helps prevent countless accidents and tragic losses of life.
Workplace Design & Environmental Controls
The layout of a facility directly impacts worker safety. In poorly designed work environments, accidents aren’t a matter of if but when.
Examples of smart workplace designs include:
- Clearly marked pedestrian lanes in warehouses with forklifts.
- Adequate lighting around machinery and loading docks.
- Barriers or guardrails near fall hazards and moving vehicles.
Regular Maintenance & Inspections
The importance of preventive machine maintenance is twofold: it ensures that equipment performs as designed and reveals defects before they become fatal. Key practices include daily equipment checks by machine operators, routine inspections by certified mechanics, and accurate maintenance logs and compliance documentation.
Machinery should never be allowed to operate in a degraded or unsafe condition simply because “we can’t afford the downtime.” Additionally, outdated tools and equipment must be promptly replaced to ensure continued safety.
Emergency Stop Mechanisms
Emergency stop buttons, cords, or switches allow operators or bystanders to instantly shut down equipment if something goes wrong. This is vital for all types of hazardous equipment, especially conveyor belts, saws, presses, and assembly line robots.
Emergency stops are one of the simplest safety features, yet many machines lack them, or they’re inaccessible when seconds count. In some cases, employees are not adequately trained in how to utilize E-stops, which can have disastrous consequences.
Holding the Line: Accountability, Prevention & Justice for Victims of Workplace Machine Accidents
Despite all we know about preventing workplace equipment incidents, workers continue to be killed or seriously injured by foreseeable and avoidable equipment failures. The question is not whether employers can prevent these tragedies but whether they will.
Employers bear the legal and ethical responsibility to implement and enforce safety measures, but too often, it’s workers and their families who pay the price for a company’s indifference. That’s where the legal system becomes a vital tool, not only to seek justice but to drive change.
When a preventable equipment-related injury or death occurs, an experienced personal injury attorney can investigate critical questions, such as:
- Was the equipment properly maintained and guarded?
- Did the employer provide adequate training and supervision?
- Were industry-standard safety measures ignored or bypassed?
- Were regulatory violations present at the time of the incident?
The answers matter, not just for compensation, but for accountability. Lawsuits and regulatory actions often uncover systemic failures that, once addressed, prevent similar incidents from happening again.
The Price of Neglect
When workplace equipment fails, it’s usually not a fluke but the final link in a long chain of preventable failures. Untrained workers, missing safeguards, ignored maintenance schedules, rushed deadlines—behind nearly every serious equipment-related injury or death is an employer who failed to uphold their legal and moral responsibility to keep their workers safe.
The law is clear: employers must provide a workplace free from recognized hazards. That includes ensuring machinery is properly guarded, maintained, and operated only by trained personnel. It means taking lockout/tagout procedures seriously, enforcing safety protocols, and refusing to prioritize production speed over human life. When employers cut corners, they don’t just break the law, they destroy lives.
For injured workers and grieving families, the consequences of this neglect are devastating: lost income, long-term disability, emotional trauma, and the immeasurable cost of a life cut short. But these tragedies do more than cause personal suffering; they expose a deeper truth that too many companies are still willing to treat safety as optional until they are held accountable.
Accountability is not just about financial compensation. It's about demanding answers. It's about uncovering systemic safety failures and making them public. It's about ensuring that the same shortcuts, the same ignored warnings, and the same dangerous habits do not claim another life.
Negligence in workplace safety is not just a regulatory issue. It’s a breach of trust. And when that trust is broken, justice must follow. No matter what.
- Categories